The system will displace concrete with reinforced plastic spheres. Advanced Building Structure Offers Real Chemistry
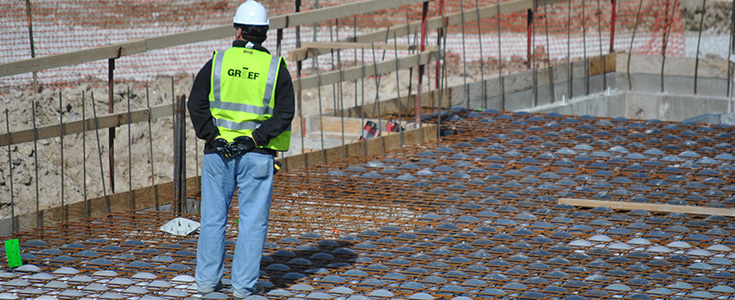
Filling the void
The voided-slab ("bubble deck") system used in the construction of the new UW chemistry building will displace concrete with reinforced plastic spheres, making the building lighter and saving approximately 1,610 cubic yards of concrete and roughly 44 tons of steel.
Contributing to building safety is a structural system featured in the new tower, a flat plate–voided concrete slab system also known as “bubble deck.” These systems, invented by Danish engineer Jorgen Breuning, have been around since the 1990s but have been more often deployed in Europe. They most often are used in hospitals and academic buildings, but they can be used in industrial and residential construction, as well. In Europe, they also are deployed in condominiums and even some parking garages.
GRAEF, the full service engineering firm, was the first to bring voided-slab systems to the United States. As explained by structural engineer Dan Windorski, a project manager for GRAEF, these are two-way voided slabs, which means the slabs can span in both directions. They are essentially made up of columns and a uniform concrete slab but without beams or drop panels, and they are the thinnest floor structure possible without post-tensioning — high-tension cables — added to the system.
The systems displace concrete that serves little structural purpose with reinforced plastic spheres, making buildings lighter and, in the case of the chemistry building, saves approximately 1,610 cubic yards of concrete, which works to about 180 fewer truckloads of concrete to the job site, and saves roughly 44 tons of steel (including reinforcing bar, or rebar). The systems are not only marginally more economical — saving 1 to 2 percent on total project cost — their floor systems offer fireproofing and they are more energy efficient and result in better building performance in terms of sound and vibration control.
As GRAEF project manager Bryant Stempski notes, the thinner floor structure offers the advantage of an additional story for commercial buildings in Madison, which face height limits. The extra floor, and the extra square footage it brings can be the difference in making a project financially viable. “You can get more floors as your structure can be thinner than some conventional buildings with a steel system,” Stempski explains. “This is about half as thick as a steel floor system.”
With the chemistry building, there will be some remodeling limitations, but McMahon notes that if spaces are property designed beforehand, that shouldn’t be an issue. “In the past with our experience, we just have a concrete slab in our existing buildings,” he notes. “So, if we want to remodel a lab after the fact and put in another sink or drain, it’s no problem to just drill a hole in the floor. Now we realize the floor itself is a very sophisticated design and you need to be careful about getting everything in there in the first place because it’s all designed as a system. We’re not going to have the same kinds of flexibilities down the line in terms of remodeling, but we just pay attention to that up front and hopefully, we’re in good shape.”
The first U.S. project to employ the voided-slab system also happens to be located on the UW–Madison campus. It’s the LaBahn Arena, which opened in 2012 at 105 E. Campus Mall and is home to the UW women’s ice hockey team.
Given their inherent advantages, why aren’t these systems used more often? Aside from the need for buy-in from multiple project stakeholders, Windorski cited promotional needs. “Marketing is the primary reason, just to get the information out there,” he states. “If you looked online, there is a lot more information than even a year ago. As a field, structural engineering is very conservative. There is a lot of responsibility to protect the safety of the general public, so it’s a very slow-moving process. It’s not the computer industry where technology is changing on a daily basis. It’s a much slower process to do something new.”
Author: Joe Vanden Plas – In Business Magazine
Photo: Mortenson Construction
Find the full article on In Business’s website here: